Bolt Torques
Bolting Materials should be of good quality, clean and well lubricated and to the site standard. The use of washers is recommended to ensure correct even torque. Bolts should be brought finger tight and then tightened through the use of a torque wrench in strict sequence of diagonally opposite pairs. This, and all subsequent torquing, of bolts should be undertaken at ambient temperature.
Please note that PTFE is suject to cold flow or “creep”. It is therefore strongly recommended that all bolts are retorqued a minimum of 24 hours after commissioning or following the initial full process cycle. The torque of all bolted joints should then be rechecked at least annually thereafter.
The following table gives recommended torque levels for ASME 150 flange to flange connections.
Nominal Bore |
Torque |
Bolts/Studs |
||||
Imp |
Metric |
Ft Ibs |
Nm |
Qty |
(Metric) |
(UNC) |
1″ |
25 |
14 |
19 |
4 |
M12 |
1/2″ |
1.1/2″ |
40 |
20 |
27 |
4 |
M12 |
1/2″ |
2″ |
50 |
35 |
47 |
4 |
M16 |
5/8″ |
2.1/2″ |
65 |
39 |
53 |
4 |
M16 |
5/8″ |
3″ |
80 |
54 |
73 |
4 |
M16 |
5/8″ |
4″ |
100 |
40 |
54 |
8 |
M16 |
5/8″ |
6″ |
150 |
80 |
108 |
8 |
M20 |
3/4″ |
8″ |
200 |
100 |
136 |
8 |
M20 |
3/4″ |
10″ |
250 |
94 |
127 |
12 |
M24 |
7/8″ |
12″ |
300 |
107 |
145 |
12 |
M24 |
7/8″ |
14″ |
350 |
134 |
182 |
16 |
M24 |
1″ |
The torque values given above are a guide; they may be exceeded by a value of 50% to effect a seal. If once this torque level has been reached a seal has not been achieved, it is likely that there is another cause.
This may be due to joint misalignment or strain, or it may be that the PTFE flare face has suffered mechanical damage. Small scratches can be removed with the use of a fine abrasive without detriment. If damage is significant, overtightening is not a solution and the component should be rejected.
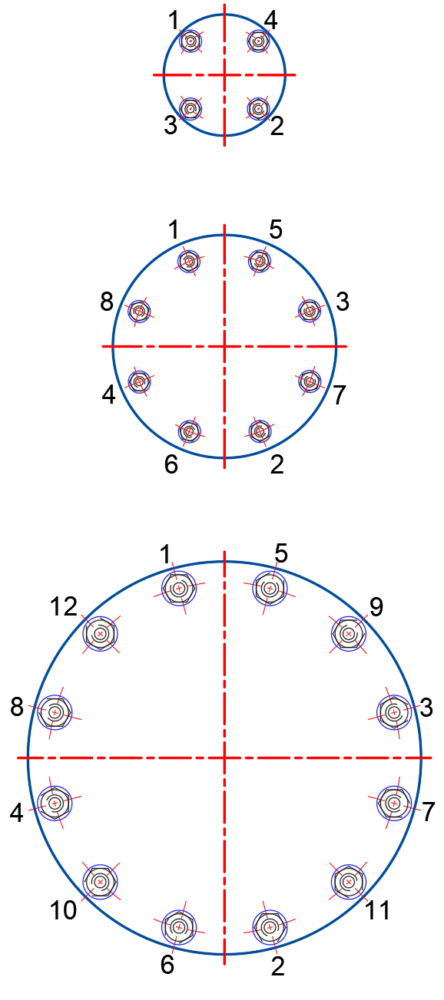